The workforce of the United States in general, and Fire & EMS agencies in particular, is undergoing some serious “seismic
shifts”: not because the earth is shifting, but because the demographics of the available labor pool are changing drastically. Bruce Tulgan, President and CEO of RainmakerThinking, Inc.®, wrote in a report he published in 2003 about one aspect of that demographic shift, the Generational Shift:
First, those of the Silent Generation (born before 1946) are gradually exiting the workforce; by 2006, two experienced workers will have left the workforce for every one who entered the workforce. Second, the Baby Boomers (born 1946-1964) are becoming the aging workforce; every day 10,000 Baby Boomers turn 55 years of age. Third, the prime-age workforce will be made up increasingly of Generation X and Generation Y (born 1978-1986). http://www.rainmakerthinking.com/genshift.doc

The passing of knowledge from one generation in the organization to the next is a critical leadership function that must be exercised if the organization is to successfully sustain itself.
While there are certainly many aspects of this shift that Fire & EMS leaders need to address, I believe one of the most critical is the communication of organizational knowledge from one generation of members to another. Steve Barth, an expert in the field of knowledge management, wrote:
“Knowledge management is the practice of harnessing and exploiting intellectual capital to gain competitive advantage and customer commitment through efficiency, innovation and faster and more effective decision-making.”
Fortunately, Steve “translated” that definition by saying, “Yet these things still account for only a fraction of the real value of your knowledge assets. Most–as much as 90 percent, by some estimations–of the real value of intellectual capital is in the heads of your knowledge workers: their skills, experience, hard-won insight and intuition, and the trust they have invested and earned in relationships inside and outside of the organization. This knowledge is even harder to evaluate, share and leverage.
So how can we in the Fire & EMS profession more proactively “capture” such knowledge before it “walks out the door” with the next retiree? Let’s take a closer look at some of our “old and reliable” information management tools: policy, procedure, and processes. Frequently, we use these terms interchangeably, but they are not synonymous at all. However, if we understand how the “fit” together, we will find that they can serve as powerful tools to help transfer organizational knowledge from one generation of members to another.
When do we need a defined process? Good question, one that is frequently asked in any business. According to Dr. Edwards Deming, the “father” of the Total Quality movement in the USA, http://www.deming.org/, an organization or group needs a defined process when these three criteria are present:
- A task or function must be repeated on a frequent basis
- A task or function must be done by multiple people
- A task or function must have a consistent outcome
Defined processes are not the same as policy or procedure, though defined processes support both. Here’s how the three compliment each other:
- Policy should state the organization’s philosophy and direction on a topic.
Policies should be broad in scope and usually do not undergo significant change on a regular basis: a well written policy should serve the organization for years on end.
- Procedure describes how a member or employee correctly complies with the stated policy. Well written procedures are an excellent “teaching tool” to help members learn the correct behavior or skill so that their actions are always in compliance with the applicable policy.
- Processes provide a very succinct description of the steps involved in following the procedure, and in turn complying with policy. Construction of process flowcharts are a very useful tool for this because they provide a great “picture” of how the task or function is performed successfully. (Most of us do better when we can see the “picture.)
Here’s an example of we can use the “3-P’s” to communicate the organization’s expectations regarding the operational preparedness for an ambulance:
- Policy – “Crews will inspect their assigned ambulance and its on-board inventory of equipment and supplies to ensure their capability to respond and provide high quality patient care. Such inspections will occur at the
beginning of the crew’s assigned tour of duty and following each response.”
- Procedure – Detailed listing of those items that must be checked along with parameters for what is acceptable, e.g., the vehicle fuel level should be 3/4 of a tank or greater or the engine oil level must be within the acceptable range on the dipstick.
- Process – Flowchart that depicts the major steps in the procedure along with decision points, i.e., what actions are required when an unacceptable situation is encountered. Example, while checking the vehicle a member finds that the warning lights do not function: the process should show what actions are necessary to correct the deficiency, e.g., take the unit out of service and send it for repairs.
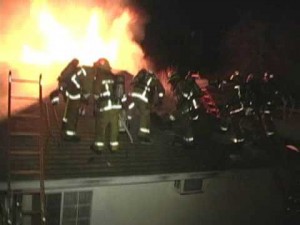
This is not a good situation. How will you ensure that your firefighters are never drawn into such an unsafe tactical position? Look no further than the 3-P’s.
Procedures and their associated processes must frequently be reviewed and updated as necessary because changes in conditions, e.g., new technology, new equipment, finances, etc., can have an influence on how the task or function must be completed in the future.